With the GIG Karasek IIoT Platform, customers have the opportunity to digitalize, monitor, and, above all, bring their production processes to the best possible operating state in order to increase their productivity and efficiency and save costs and resources.
Data exchange as a win-win situation
Industry 4.0 is based on the efficient collection, analysis, and use of data, as well as the secure exchange of this data between system operator and supplier. Although many of our customers still have concerns about data security and loss of know-how, which of course need to be allayed, the benefits of implementing Industry 4.0 solutions in this day and age are undisputed.
- Specialist knowledge: With the data connection of the system supplier, the customer receives additional expert knowledge to optimize operating processes and achieve the best possible results.
- Smart additional benefits: Data processing can generate considerable added value and significant cost savings for the system operator (see smart services).
- Remote support Access via remote maintenance modules enables process monitoring and intervention without the need for an external expert to be physically present in the plant.
- Further development: The system builder receives valuable feedback for validating designs and can adapt the system to changed parameters.
Industry 4.0 thus creates a win-win situation in which both operators and system builders benefit. The result is valuable and transparent cooperation that paves the way for a successful future and progress in plant engineering.
Figure 1: Industry 4.0 involves the use of advanced technologies, such as the Internet of Things (IIoT – Industrial Internet of Things), artificial intelligence, and machine learning, to make production more efficient and flexible. The IIoT platform serves as a central infrastructure for the collection, processing, analysis, and display of digital data. It integrates various components, such as devices, networks, cloud services, databases, and analytics tools to enable data flow and provide insights for optimizing industrial processes. In-house illustration © GIG Karasek
IIoT Platform as a strategic Industry 4.0 interface
As an essential component of Industry 4.0, the Industrial Internet of Things (IIoT) networks machines, equipment, and systems by means of sensors and other IIoT components.
So what does the GIG Karasek IIoT platform offer?
- It serves as the central interface for data exchange and cooperation with the customer.
- By integrating IIoT devices – so-called “edge devices” – into the platform, data is collected, transmitted, and analyzed in real time.
- Relevant information can be extracted, trends identified, and predictive analytics performed. In other words, our smart services can be used.
The integration of IIoT technology is proving to be extremely useful for individual machines, large-scale plants, and especially stand-alone systems that are operated independently of other trades. The latter often have fewer personnel with specific process know-how available, which makes optimized system operation more difficult in this regard, especially in smaller companies.
© Winterleitner
"Intelligent networking of machines and data optimizes the entire production process and enables our customers to increase their operational efficiency to an unmatched level. The IIoT opens the door to real-time information, accurate analytics, and proactive decision-making to maximize plant performance, minimize downtimes, and optimize the total cost of ownership. With GIG Karasek and the IIoT as allies, our customers can confidently shape the future of industrial manufacturing and gain a competitive advantage that sets them apart from the competition."
Andreas Schnitzhofer, Managing Director, GIG Karasek
Cornerstones of the GIG Karasek IIoT Platform:
1. User-friendliness through intuitive and transparent operability
The IIoT platform is deliberately designed to be simple and intuitive to use, in order to ensure smooth use and to break down barriers when dealing with data and the Internet.
Even people without special IT expertise can control the platform. By presenting data processing and storage in a transparent and comprehensible way, we ensure that customers have a clear understanding of what happens to their data and where it is stored.
Figure 2: Dashboard of the GIG Karasek IIoT platform – example display and management of production facilities. © Autonoma
2. Certified edge devices and secure data transmission
The connection to the IIoT platform is established by an edge device that is integrated into the customer's process control system as a physical component.
- Essentially, the device acts as an intermediary between the sensors/devices and the IIoT platform.
- It collects data from sensors or other devices in real time, processes it, and forwards it to the platform in compliance with all relevant safety precautions.
- There, the data is further analyzed, processed, and used for various applications.
When using the IIoT platform, we attach great importance to security and data protection. All communication is done via MQTT, a secure protocol, as well as TLS 1.3 (highest standard).
In addition, all edge devices have certificate management. These certificates are used to verify the identity of a device, encrypt data communications, and ensure the integrity of transmitted data.
Figure 3: Test standards © Autonoma
We also rely on strict access controls to ensure that only authorized persons can access the data. This means that the customer retains full control over their data and determines which access rights are granted to the GIG Karasek team. This ensures a high level of security and enables the customer to maintain ownership of their data.
3. Cloud storage: Basis for the analysis of long-term trends
By using cloud storage, data can be collected over a longer period of time and sound conclusions can be drawn about performance and behavior patterns as well as long-term trends.
A concrete example is the tendency of equipment getting dirty, especially fouling. Short-term observations show considerable fluctuations. By extending the period under consideration and performing a more comprehensive analysis, meaningful evaluations can be created that reveal relevant long-term trends.
This advanced analysis allows us to better understand how soiling develops over time and how it affects system performance. This allows more targeted measures to be taken to minimize the effects of soiling and optimize long-term system performance.
Digitalized devices enable smart services
The GIG Karasek Digitalization Platform opens up new possibilities for optimizing the performance level of systems, making predictions, and deriving strategic recommendations for action. Customers have the opportunity to make optimizations, organize predictive maintenance, obtain information on critical parameters, increase downtimes, and improve system availability.
Depending on customer requirements, GIG Karasek offers the following smart services:
- Digital twin (virtual model of a system)
- Condition monitoring (observance and analysis of process parameters)
- Predictive maintenance (for when servicing is needed)
- Optimization as a service (improvement of production sequences and energy consumption)
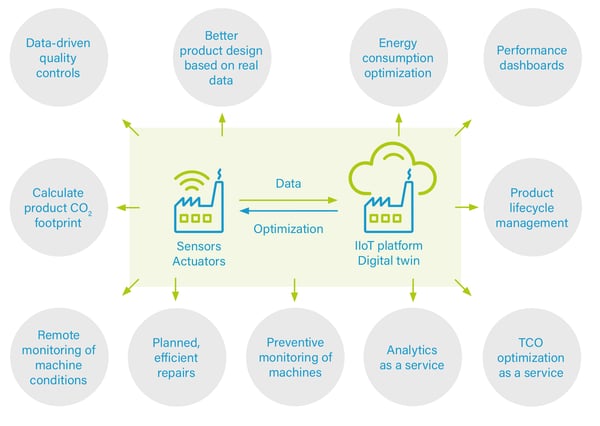
Figure 4: IIoT enables a wide range of smart services. In-house illustration. © GIG Karasek
Digital Twin – powerful linking of real and virtual system worlds
Probably the most extensive application in the field of digitalization currently consists of mapping equipment or entire systems as virtual "digital twins" and storing them with comprehensive documentation.
Real-time information through continuous synchronization
An illustrative example is the digital twin of a thin-film device. Relevant data on components such as mechanical seals, motors, internals, or wiper types are mapped as a duplicate of the machine and are available for a wide range of applications.
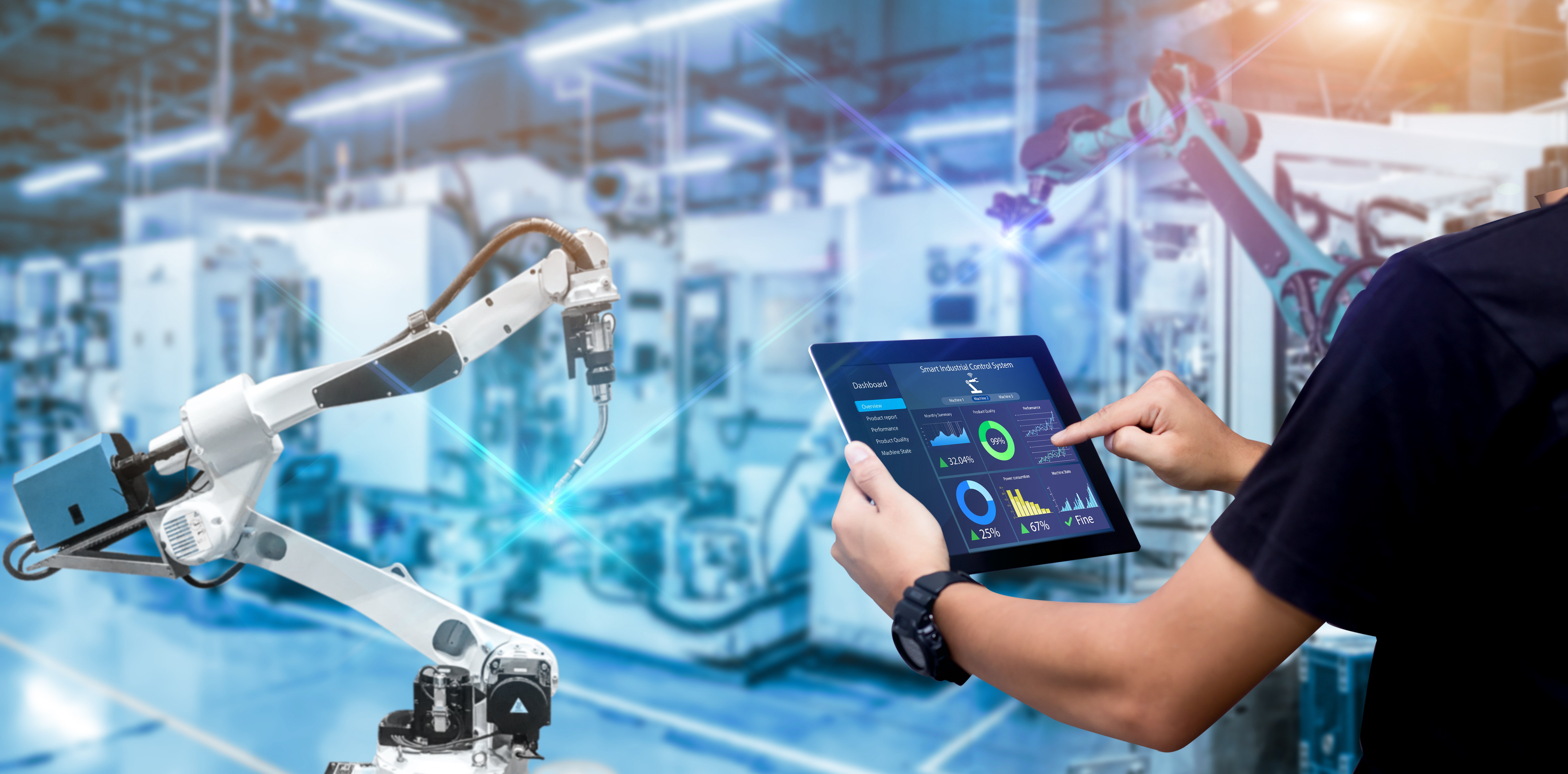
© Adobe Stock
Collected information can be accessed in real time using tablets, cell phones or data glasses, and specific actions can be taken as a result. For example, spare parts can be ordered directly on site in the production hall.
However, the digital twin opens up a much wider range of applications. In addition to improved monitoring, analysis, and control of the system, it also enables simulation of different scenarios, optimization of processes, and prevention of operational problems through continuous synchronization with the real counterpart. The main goal here is to maximize the performance, efficiency, and reliability of the twin in the real system world.
Digitalization in the pilot plant: digital twin for customer trials
On our platform, the GIG Karasek pilot plant is available as a practical example of an innovative digital twin and enables realistic process imitation and practice-oriented evaluations. Together with our customers, tests can be tracked online, trends read out, and calculations performed. As a next step, we plan to integrate our own manufacturing into the IIoT platform.
Condition monitoring: early warning system for optimum operation
Condition monitoring refers to the continuous monitoring and evaluation of the condition of machinery and equipment in order to detect potential problems at an early stage and take preventive action. Various parameters such as vibrations, temperatures, pressure conditions, noises, or electrical signals are continuously recorded and analyzed.
Condition monitoring immediately detects changes in the operating behavior or the changed condition of components or devices. As soon as critical limit values (e.g. defined values for vibrations, speeds, pressure, or temperature) are exceeded, an alarm is triggered. Potential malfunctions, signs of wear, or defects can thus be identified at an early stage and appropriate measures taken.
This proactive approach enables the avoidance of failures, the prevention of potential damage, and the early identification of trends that indicate potential for improvement.
Figure 5: Measurement data monitoring – Example illustration of a process plant © GIG Karasek
Predictive maintenance: future-oriented problem detection and optimal maintenance planning
Predictive maintenance is a service for effective maintenance of equipment and machinery that uses algorithms and machine learning models to analyze data and make predictions. Based on these predictions, the optimal time for maintenance measures can be determined.
Compared to condition monitoring, which mainly monitors current conditions, predictive maintenance relies on analyzing historical data to predict future problems. This allows maintenance activities to be planned and executed before a failure occurs, resulting in higher plant availability, lower maintenance costs and more efficient use of resources.
For example, if a rolling bearing is nearing the end of its service life, the system can automatically trigger an order or generate a reminder to have the corresponding spare part available in time.
If the customer sources the spare part directly from GIG Karasek, the ordering process is automated by our EAP (Enterprise Asset Planning) integration. We have all the relevant data, such as order numbers and model numbers, to facilitate the ordering process. In this way, an efficient and automated system is created.
Optimization as a service: maximum performance, even when the parameters change
GIG Karasek provides state-of-the-art equipment that is optimally adjusted to the respective requirements of the application. However, the general conditions in industrial production are subject to constant change. For example, the material supplied (feed) or the requirements for the end product may change. The optimization of the system must be adjusted accordingly, which often cannot be implemented consistently and efficiently in practice.
OaaS (Optimization as a Service) provides valuable insights into a system's operational behavior and characteristics. It is based on a combination of data analysis and joint meetings to identify optimization potential and make appropriate adjustments in a targeted manner. The aim again is to keep the system's performance, efficiency, and yield at the highest possible level – even when requirements change – while reducing costs.
Conclusion: Industry 4.0 – the key to a competitive edge
Companies that actively integrate Industry 4.0 into their business processes can gain a significant competitive edge. As an experienced and innovative partner in thermal separation and CO2 utilization technology, we offer our customers the opportunity to improve their operations, reduce costs, and significantly increase the efficiency of their systems. Close collaboration and secure data exchange allow us to develop solutions that meet each customer's unique requirements and budgetary constraints.
We look forward to accompanying you on your way to a successful future.
Visit our newsroom!
Here you can find the latest NEWS, our EVENT CALENDAR or further INSIGHTS featuring our key topics.
On the topic of our IIoT platform we have published the following articles so far:
GIG Karasek Pay-Per-Use: Flexible Financing for Plants in Dynamic Markets