To make the best use of industrial waste heat, both open and closed heat pump systems are employed, each offering specific benefits and application areas. The following article explains the technological distinctions and uses CompriVAP and VarioVAP to introduce an innovative heat pump concept by GIG Karasek that significantly enhances plant efficiency and enables the combined utilization of smaller heat streams.
Contents
1. Operating principle: open vs. closed heat pump systems
2. Differences in heat transfer and efficiency
4. Comparison of compressor technologies
5. Waste heat temperature and heat pump selection
6. Overview of advantages and disadvantages
7. CompriVAP & VarioVAP: two solutions for maximized waste heat utilization
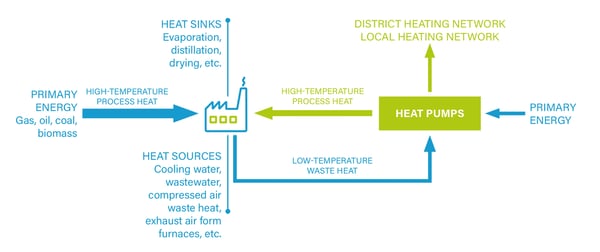
Figure 1: The topic of industrial heat pumps is more relevant than ever, especially in the areas of waste heat utilization and heat recovery. © GIG Karasek
1. Operating principle: open vs. closed heat pump systems
The key difference between open and closed heat pump systems lies in the method of heat transfer and process configuration.
1. Closed heat pump systems
Closed systems use a refrigerant as an intermediate medium to absorb, transport, and raise heat to a higher temperature level within a closed circuit:
1. Heat exchanger (evaporator): The refrigerant absorbs energy from the waste heat source and evaporates.
2. Compressor: Compression increases the pressure and temperature of the refrigerant vapor.
3. Heat exchanger (condenser): The refrigerant transfers the absorbed energy to the working medium (e.g. hot water or steam) and condenses.
4. Expansion valve: The pressure and temperature of the refrigerant drop, allowing it to absorb energy once again.
Figure 2: The refrigerant circulates in a closed-loop system that operates continuously and requires the use of two heat exchangers. © GIG Karasek
2. Open heat pump systems
In open heat pump systems, there is no refrigerant cycle. Instead, the medium from the waste heat source also serves as the working medium (steam), which is compressed to a higher pressure and temperature level (see Fig. 3 – example of mechanical vapor recompression). Alternatively, the energy from the waste heat source is transferred to the working medium (water), causing it to evaporate, after which it is compressed to the target pressure.
1. Heat exchanger (evaporator): The waste heat source heats water in the evaporator, generating steam.
2. Compressor: The steam is directly compressed to a higher energy level.
3. Energy transfer: The compressed steam transfers its heat to the process, e.g. for steam generation or industrial applications.
4. Condensation and recirculation: After releasing its heat, the steam condenses and can be reintroduced into the cycle.
Since no refrigerant is used as an intermediate medium, the separate refrigerant cycle is eliminated, and only a single heat exchanger is required.
Figure 3: Schematic of mechanical vapor recompression based on the open heat pump principle: process vapor (vaporous distillate) is compressed by an electrically driven compressor and reused to heat the evaporator. © GIG Karasek
2. Differences in heat transfer and efficiency
In a closed system, two heat exchangers are required to transfer energy from the heat source to the working medium. Because heat transfer always depends on a temperature gradient between two media (heat flows only from a warmer to a cooler medium), this inherently leads to efficiency losses:
- First transfer: From the heat source to the refrigerant – this introduces an initial temperature difference and corresponding efficiency loss.
- Second transfer: From the refrigerant to the working medium – this creates another temperature difference and a second efficiency loss.
In contrast, an open system eliminates the need for a second heat exchanger, as the medium absorbing energy from the heat source is also the working medium itself. This setup requires only a single temperature difference, resulting in higher overall system efficiency.
Example: generation of 100°C steam
Closed system:
- The refrigerant must be heated to 105°C to raise the steam temperature to 100°C.
- Energy loss: 5°C (105°C → 100°C)
Open system:
- The steam is heated directly to 100°C.
- No energy loss
Industrial relevance
In industrial settings where large amounts of energy are transferred, open systems offer significant potential for energy and cost savings due to their higher efficiency. As a result, open heat pump systems are the preferred choice in industrial applications – provided that the operating conditions, particularly the temperature of the heat source, are suitable.
Figure 4: Comparison of open and closed heat pump systems in terms of heat transfer and efficiency. © GIG Karasek
3. The refrigerant factor
In industrial applications with high energy demands, closed heat pump systems require large volumes of refrigerant, which pose significant safety risks and incur substantial costs:
- Safety risks: Refrigerants are often toxic, flammable, or explosive. Even minor leaks can be difficult to manage due to the large circulating volumes and may lead to serious consequences.
- High costs: Procuring, operating, and disposing of refrigerants is expensive. Additional costs arise from safety measures, maintenance, and leak mitigation.
As heat pump systems scale up, operational safety becomes increasingly critical. Consequently, many industrial operators avoid closed systems, viewing the associated risks, maintenance burden, and ongoing expenses as prohibitively high.
Open heat pump systems offer a compelling alternative: they eliminate the need for refrigerants, reduce risks and costs, and increase efficiency by doing away with the second heat exchanger.
4. Compressor technology compared
Open and closed heat pump systems differ significantly in their technological design – especially in terms of the compressor technologies used and the associated pressure ratios. While closed systems rely on refrigerants and high pressure differentials, open systems use direct steam compression and multi-stage compression to minimize energy losses and enhance efficiency.
Closed systems: high pressure differentials
In closed heat pump systems, refrigerants circulate continuously: they evaporate at low pressure and condense at high pressure. To manage these pressure differences, high-performance compressors such as piston or screw compressors are used.
While these compressors are capable of generating large pressure lifts, they also incur significant energy losses due to friction, heat dissipation, and refrigerant overheating. The greater the pressure differential, the higher the losses. These efficiency losses directly impact system performance and operating costs, ultimately resulting in lower overall system efficiency.
Open systems: moderate pressure differentials
Mechanical compression using radial compressors (centrifugal compressors) is the preferred choice for industrial applications. Compared to closed heat pump systems, they operate more efficiently by managing pressure differences with lower energy losses – especially at high volume flow rates and moderate pressure ratios, which are typical in many industrial processes. However, this technology requires a minimum threshold of available waste heat, making it particularly suitable for large-scale industrial use.
Multi-stage compression and intercooling for greater efficiency
To achieve larger pressure lifts efficiently, open heat pump systems utilize multi-stage compression. In this setup, pressure is increased step by step through a series of sequential radial compressors. Compared to a single compressor handling a large pressure or temperature lift in closed systems, this approach delivers significantly higher efficiency.
Additional efficiency gains are achieved through intercooling of the steam after each compression stage. This prevents overheating and maintains the steam in a saturated state, allowing compression to occur with lower energy input – a key advantage over closed heat pump systems, where cooling is far more complex and less effective.
Industrial relevance and application areas
Thanks to their high performance and scalability, radial compressors are particularly well suited for large-scale industrial processes involving substantial energy flows – whether in waste heat recovery, steam generation, or the provision of process heat. Their efficiency and cost-effectiveness make them a key technology for more sustainable industrial heat supply.
Figure 5: Comparison of compressor technologies in open and closed heat pump systems with regard to heat transfer and efficiency. © GIG Karasek
5. Waste heat temperature and heat pump selection
For harnessing waste heat with heat pumps, low-temperature streams that can no longer be used effectively in direct heat exchangers (e.g. for heating water or air) are of particular interest. The temperature of the waste heat determines which type of heat pump system is suitable. Open systems are better suited for higher temperatures, while closed systems can also utilize lower temperature levels – though typically with reduced economic efficiency.
Open heat pumps: high efficiency with suitable waste heat sources
Open heat pump systems use water vapor as the working medium and require a minimum temperature level from the waste heat source. This is due to the limited pressure differential that a compressor can generate, as well as the direct correlation between pressure and temperature. Therefore, a sufficiently high waste heat temperature is essential to ensure efficient operation.
Steam generation under vacuum
The boiling point of water depends on pressure. At high altitudes, where atmospheric pressure is lower, water boils at temperatures below 100°C. Open heat pump systems apply the same principle: by reducing the pressure, water vapor can be generated at lower temperatures.
For example, if the waste heat source is at 80°C, lowering the pressure in the evaporator allows steam to be generated at 75°C. This requires a vacuum comparable to conditions found at high altitudes. However, the practical application of this principle is limited.
Temperature and pressure limits
The efficiency of open heat pump systems is constrained by both physical and economic constraints:
- The lower the temperature of the waste heat source, the lower the required pressure.
- The lower the pressure, the lower the steam density and the higher the steam volume.
- Large steam volumes at low pressures require large-scale equipment, which becomes economically unfeasible or technically impractical below a certain vacuum threshold.
- The physical and economic limit is generally considered to be a vacuum below 100 millibars.
These limits define the minimum temperature requirements for the waste heat source:
- Liquid media should have a temperature of at least 70°C, as at temperatures below this the required vacuum is too low and the vapor volume too large.
- For condensing media, the minimum dew point temperature should be around 60°C.
Thus, open heat pump systems are particularly well suited for industrial applications where large volumes of low-temperature waste heat are available and are often discharged unused via wastewater or exhaust air.
Closed heat pumps: advantages at very low temperatures
When the temperature of the waste heat source is too low for open systems, closed heat pumps provide a viable alternative. Their key advantage lies in the thermodynamic properties of refrigerants, which can absorb heat even at comparatively low temperatures.
Applications and limitations
Closed heat pumps are particularly advantageous for moderate temperature lifts – for example, generating hot water for in-plant use or supplying local and district heating networks. However, they become inefficient when very low temperatures need to be raised to very high levels, such as for steam generation.
From an economic standpoint, closed systems are most viable for temperature increases in the range of 30–50 K (Kelvin) – for instance, from 40°C to 80°C. Larger temperature lifts typically result in diminished efficiency and are generally considered uneconomical.
6. Overview of advantages and disadvantages
Open heat pump systems are particularly well-suited for handling large volumes of waste heat at sufficiently high temperatures. They offer high efficiency, eliminate refrigerant-related risks, and reduce operating costs. In contrast, closed systems are better suited for lower temperature ranges but typically incur higher operating costs and efficiency losses due to the refrigerant cycle. The choice between systems depends on the specific requirements of the waste heat source, temperature levels, and industrial processes. Nevertheless, both technologies offer significant potential for improving energy efficiency and reducing CO₂ emissions.
To further optimize the advantages of open systems and enable the utilization of smaller waste heat sources, GIG Karasek has developed specialized heat pump systems that are setting new standards in industrial applications. The following section provides a brief overview of these systems and their technological features.
Figure 7: Advantages and disadvantages of open and closed heat pump systems in industrial applications. © GIG Karasek
7. CompriVAP & VarioVAP: two solutions for maximizing waste heat utilization
Rising energy prices, uncertain gas supplies, and increasingly stringent climate targets are forcing industry to rethink its energy strategies. In this context, the utilization of industrial waste heat is becoming ever more critical. Technologies such as CompriVAP and VarioVAP from GIG Karasek offer innovative solutions to harness waste heat efficiently, cut costs, and reduce CO₂ emissions at the same time.
CompriVAP: converting waste heat into usable process steam
The CompriVAP system utilizes the principle of Mechanical Vapor Recompression (MVR) to recover and reuse steam from low-temperature waste heat. Electrically driven compressors draw in (vacuum) steam, increase its energy level by compressing it, and thereby convert waste heat into high-quality process steam.
- Easy integration: CompriVAP can be seamlessly integrated into existing systems and can be precisely tailored to the customer’s specific needs through its flexible number of compressor stages.
- Wide range of heat sources: The system handles both warm liquids and vapor or gases. When using heat sources containing components that should not be present in the process steam, the thermal energy is first transferred to water, which is then evaporated under vacuum conditions.
- Adaptable heat exchange: The heat transfer method is specifically matched to the unique characteristics of the heat source and the desired properties of the process steam.
- High cost-effectiveness: The system significantly boosts energy efficiency and offers substantial potential for reducing operating costs (OPEX).
- Proven technology: The underlying technology is well-established and has demonstrated its effectiveness in large-scale industrial applications.
The largest CompriVAP system to date will be implemented in cooperation with BASF SE in Ludwigshafen. With a thermal capacity of up to 50 MW and an 11-stage compressor system, it will be the most powerful industrial heat pump system in the world.
Areas of application
CompriVAP is especially well-suited for energy-intensive industries such as chemical manufacturing, steel production, pulp and paper, and food processing. Typical applications include the reuse of wastewater or process condensate, as well as the recovery of heat from exhaust air or flue gases. Significant waste heat potential can be tapped from processes such as washing and drying, as well as evaporation and distillation operations.
Figure 8: Example layout of a CompriVAP system featuring a multi-stage compressor unit. © GIG Karasek
VarioVAP – A centralized solution for multiple waste heat sources
The VarioVAP system enables the simultaneous utilization of multiple diverse heat sources within a centralized solution – unlike the CompriVAP system, which is designed for a single heat source. At the heart of the system is a state-of-the-art falling-film plate evaporator that centrally collects various waste heat streams without mixing vapors and condensates. Instead of deploying separate heat pumps for each source, the VarioVAP system combines all heat sources into a single heat pump unit.
Key advantages of the VarioVAP system
- Efficient waste heat utilization: Smaller waste heat streams that would otherwise be economically unviable can be profitably harnessed by consolidating them into a single system.
- Increased plant efficiency: Centralizing heat sources reduces energy losses and enhances the overall economic viability of waste heat recovery.
- Application flexibility: VarioVAP can be integrated into existing processes or used as a standalone heat exchanger solution.
- Safe media handling: Separate flow paths within the evaporator enable the safe processing of even explosive vapors.
- Reliable partial load operation: If one heat source fails, the system continues to utilize the remaining waste heat streams effectively.
Areas of application
The VarioVAP system enables near-complete utilization of waste heat – achieving a “zero heat waste” approach. Even low-grade waste heat streams that previously went unused can be converted into fresh steam. In addition to its use in energy-intensive industries, the system is ideally suited for industrial parks: by consolidating waste heat streams from multiple companies, a substantial usable potential emerges that VarioVAP can tap into with maximum efficiency.
Figure 9: Example illustration of a VarioVAP system featuring three distillation columns, with vapors supplied to the falling film evaporator via separate lines. The generated steam is then compressed through multiple stages to increase its energy level. © GIG Karasek
Conclusion: a step toward sustainable process heat supply
Industrial waste heat recovery is no longer a ‘nice-to-have’. It's an economic necessity. CO₂ pricing is set to rise sharply in the coming years, and with the onset of open emissions trading in 2027, fossil fuel costs are expected to soar. With CompriVAP and VarioVAP, companies have access to powerful, scalable, and cost-effective solutions to efficiently harness industrial waste heat and position themselves optimally for the future. In addition to substantial OPEX savings, many projects become even more economically attractive through government funding. Especially in times of rising CO₂ prices and uncertain energy supplies, these innovative heat utilization technologies represent a future-proof investment.
Visit our newsroom!
Here you'll find latest NEWS, our EVENT CALENDAR and additional INSIGHTS on key topics.
We’ve also published the following articles on the topic of waste heat utilization:
Efficient Use of Waste Heat: Industrial Heat Pumps as a Driving Force of the Energy Transition
CompriVAP Heat Pump Solution: Turning Waste Heat into Value